Energy and Oil
The energy and oil industry operates across a vast spectrum of challenging environments, from the extreme cold of arctic regions to the intense heat of downhole drilling and refining processes. Precise temperature control is not just a matter of efficiency; it is fundamental to ensuring operational safety, equipment reliability, material integrity, and regulatory compliance across exploration, production, transportation, and refining. Maintaining specific temperatures is vital for everything from preventing pipeline blockages and optimizing refining reactions to testing materials for use in harsh conditions. Our robust range of temperature control solutions, including high-precision circulators, chillers, and environmental chambers, is designed to meet the demanding requirements of the energy and oil sector. We provide the reliable thermal management needed for critical material testing, process optimization, equipment validation, and simulating real-world operating conditions, contributing to safer, more efficient, and more reliable operations.
Navigating Thermal Extremes in the Energy and Oil Sector
The energy and oil industry faces unique and significant challenges related to temperature at every stage of its complex value chain. Operations span diverse geographical locations with ambient temperatures ranging from sub-zero to scorching heat. Furthermore, the processes involved often generate or require extreme temperatures and pressures.
Consider the pervasive impact of temperature:
- Upstream (Exploration & Production): Equipment used in drilling and extraction must withstand high downhole temperatures and pressures. Materials used in offshore platforms or arctic exploration need to retain their properties in extreme cold. Simulating these downhole conditions is crucial for testing tools and components.
- Midstream (Transportation & Storage): Pipelines transporting crude oil, natural gas, or refined products are exposed to varying environmental temperatures. For viscous fluids like heavy crude, maintaining elevated temperatures is necessary to ensure flow and prevent waxing or blockages. Materials used in pipelines and storage tanks must resist brittle fracture in cold climates.
- Downstream (Refining & Petrochemicals): Refining processes involve complex chemical reactions that require precise temperature control for optimal yields, product quality, and energy efficiency. Distillation columns, reactors, and heat exchangers all rely on accurate temperature management. High temperatures are also involved in processes like catalytic cracking and steam injection.
Across all these segments, the performance and integrity of materials – metals, elastomers, polymers, and composites – are highly temperature-dependent. Components can degrade, lose strength, or become brittle if exposed to temperatures outside their design limits. Accurate material testing under simulated operating temperatures, including low-temperature impact testing for pipelines and high-temperature aging tests for seals and other components, is therefore essential for preventing failures and ensuring safety.
Furthermore, critical equipment, from pumps and valves to sensors and electronic controls, must be validated to function reliably in the specific thermal conditions they will encounter. Deviations in temperature can lead to operational inefficiencies, equipment damage, environmental hazards (like spills or emissions), and pose significant safety risks to personnel. Reliable temperature control and the ability to simulate operational temperatures for testing are indispensable for managing these risks and ensuring continuous, safe, and efficient energy and oil operations.
Our Solution: Engineered Temperature Control for Energy and Oil Applications
We provide specialized temperature control solutions built to withstand the demanding conditions of the energy and oil industry and deliver the precision required for critical processes and testing. Our equipment enhances reliability, supports safety standards, and contributes to operational efficiency across the sector.
Here’s how our temperature control devices address key needs in the energy and oil industry:
-
Material Testing for Extreme Environments:
- Need: Testing the mechanical properties and fracture toughness of materials (especially metals and polymers) at the extreme low or high temperatures they will encounter in service (e.g., pipelines in arctic regions, seals in high-temperature wells).
- Solution: Our refrigerated circulators and cooling baths provide precise low-temperature conditioning for impact tests (Charpy, DWTT) and other mechanical tests, ensuring materials perform reliably in cold climates. Our heating circulators can be used for elevated temperature material testing, such as simulating the heat exposure of elastomers or coatings used in high-temperature applications.
- Example: Using a low-temperature cooling bath to condition pipeline steel specimens for Charpy testing at -50°C verifies that the material remains ductile and resistant to brittle fracture in freezing conditions.
-
Simulation of Downhole and Process Conditions:
- Need: Simulating the high temperatures and pressures found in downhole environments or specific refining processes to test the performance and reliability of equipment and components.
- Solution: While high pressure requires specialized vessels, our high-temperature heating circulators can provide the precise thermal input to simulate elevated temperatures in laboratory test setups designed to replicate downhole or process conditions for testing tools, sensors, or materials.
- Example: A heating circulator can maintain a test fixture at 150°C while a downhole sensor prototype is evaluated under simulated pressure, validating its performance in a high-temperature well environment.
-
Equipment and Component Validation:
- Need: Testing the functionality and durability of critical equipment (electronics, sensors, valves) under simulated environmental temperature extremes encountered in diverse operational locations.
- Solution: Our climate chambers can simulate wide-ranging ambient temperatures (and often humidity) to rigorously test equipment reliability in conditions replicating arctic, desert, or tropical environments before deployment. Heating and refrigerated circulators can also be used to cycle components through operational temperature ranges.
- Example: Placing electronic control units for an offshore platform in a climate chamber and cycling the temperature from -20°C to +50°C ensures they function reliably across expected ambient conditions.
-
Laboratory and Pilot Scale Process Control:
- Need: Maintaining precise temperatures for research, development, or quality control in laboratory settings, including small-scale refining simulations or fluid property analysis.
- Solution: Our heating and refrigerated circulators and water baths provide accurate and stable temperature control for beakers, reactors, viscometers, and other lab equipment used in R&D and quality control for oil and gas products and processes.
- Example: A research chemist analyzing the viscosity of a new lubricant under varying temperatures uses a refrigerated circulator connected to a viscometer jacket to maintain precise test temperatures.
-
Cooling for Processes and Equipment:
- Need: Providing cooling for various processes, analytical equipment, or smaller-scale plant operations.
- Solution: Our chillers offer reliable and efficient cooling, whether for cooling laboratory equipment, removing heat from smaller process streams, or providing temperature control for specific instruments.
- Example: A chiller provides cooling water to a condenser in a laboratory distillation setup used for analyzing hydrocarbon mixtures.
Benefits to the Energy and Oil Industry:
- Enhanced Safety: Ensuring materials and equipment perform reliably in extreme conditions reduces the risk of failures and incidents.
- Improved Reliability: Validating equipment and materials under simulated operational temperatures increases confidence in their long-term performance.
- Optimized Efficiency: Precise temperature control in processes improves yields, reduces energy consumption, and prevents issues like pipeline blockages.
- Regulatory Compliance: Our systems support testing methodologies that meet stringent industry standards and regulatory requirements.
- Reduced Costs: Preventing failures, optimizing processes, and streamlining testing contribute to significant cost savings.
By partnering with us, the energy and oil industry gains access to the precise temperature control technology needed to navigate thermal challenges, ensuring the safety, reliability, and efficiency of their critical operations worldwide.
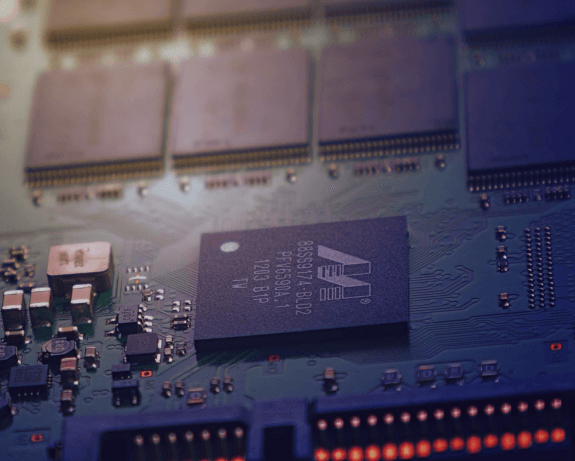
Testimonials
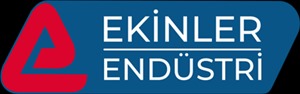
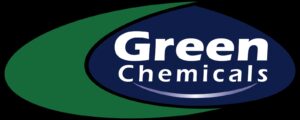
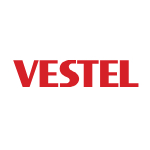
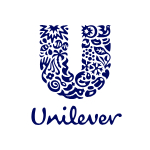
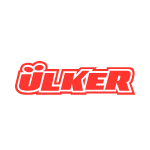
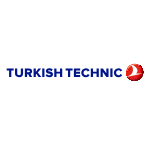
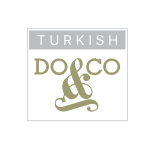
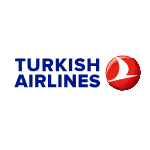